In this blog, I will be discussing the energy savings associated with a 2165 square foot home in Tulsa Oklahoma. I would like to begin by explaining the process that led to our diagnosis. Firstly, we were called out to a home because a company diagnosed that the compressor was going out and it would be best to upgrade the outdoor condenser to a new system. The homeowner was gathering estimates and I found myself giving recommendations and options for their, initially asked, system replacement. The homeowner did complain about excessive dust accumulation on countertops and furniture as well as high utility costs when asked. After visually looking over the equipment to be replaced and the ductwork in the attic, I determined it would be best to conduct a load calculation and energy audit on the home. Upon completion of the load calculation and the energy audit, the following information was presented to us.
Up Front Pricing:
The total cost of this project was $19,548 and included removal of attic insulation, sealing the home, replacing the HVAC system with an 18 SEER 3.5-4 ton dual stage compressor and 97% AFUE Goodman System, replacing the tank water heater with a State by Takagin Tankless Gas Water Heater, Replacing the entire return air duct system in the attic, Aerosealing the return and supply air duct system and insulating the attic to R-38+ with Owens Corning Fiberglass Insulation. The homeowner received a rebate of $4,100 up front from the electric company. The homeowner paid $7,849 down and received $800 in rebates from the gas company within 4-6 weeks after installation. After installation, the homeowner was responsible for monthly payments of $130.81 per month for 60 months at 0% interest.
Energy Savings on a Month to Month Basis:
The utility savings associated with the following project amounted to $830 for the first 12 months after installation. Though the monthly payments at 0% interest amounts to $1569.72 per year, it yielded a savings of $830 per year. So the homeowner is actually paying $61.65 per month for the upgrades to their home rather than the actual $130.81. And, of course, after 5 years, the homeowner will no longer have to make payments. Aside from the energy savings, the homeowner has reported a substantial increase in the comfort level of the home, less frequent filter changes, and way less dust. The difference is noticeable and was reported to have been well worth it.
First we were able to measure the home and determine that the square footage was 2,165 square foot and the cubic volume was 17,320 cubic feet volume. This is important because the International Energy Conservation Code sets guidelines based on the cubic volume and square footage of a home.
Secondly, we were able to capture the leakage rate of the home utilizing a blower door test. To learn more about blower door testing click here. The image below reflects the test in leakage rate of the home. Some of the major areas of leakage found within this particular home were in the duct system itself as well as a water heater closet that contained a 30 gallon gas water heater with large combustion air pipes communicating with the vented attic space. Another area of leakage was found to be in the top wall plates where the lathe and plaster meet the framework of the home as well as where the electrical wiring for the home went through the top wall plates to the recepticles and switches. Aside from that, all light fixtures in the home were extremely leaky.
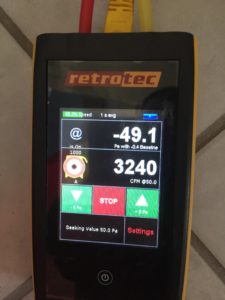
Next, upon visual inspection of the ductwork, it was determined that it was poorly insulated and leaky. Because the return air duct system was located in the attic, the hot air in the summer mixed with the dust that naturally settles in all ventilated attics was being drawn into the ducts through leakage and delivered to the home. It was recommended to replace the return air duct system, insulate with R-8 insualtion and Aeroseal both the supply and return air duct system.
The attic was very poorly insulated and had maybe 1″ to 3″ of old cellulose insulation blown in 50 years ago. It was recommended to insulate the home to R-38+. The Department of Energy sets the attic insulation standard in the United States. R-38 is the recommended insulation level in our zone, Oklahoma, of the United States
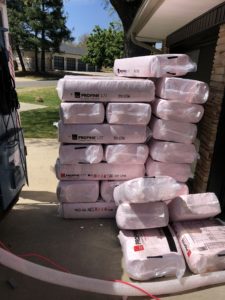
It was also recommended to upgrade the HVAC System to a newer, more, energy efficient model. They did have a 13 SEER Air conditioner installed with a Variable Speed Motor 80% AFUE Furnace installed originally. We proposed a 2 stage 18 SEER Communicating system by Goodman with a 97% AFUE Furnace with a Variable Speed Motor and Modulating Gas Valve.
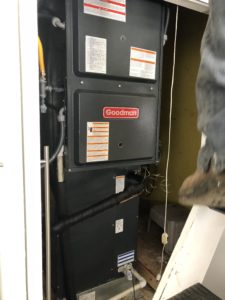
With communicating equipment it is highly recommended to install a communicating thermostat. With this particular system we recommended the CTK04 Thermostat. This particular thermostat set up is 4 wire and offers dehumidification, remote access and programming.
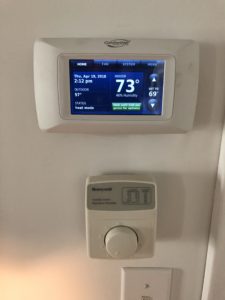
Last but not least, it was recommended to replace the tank water heater with a tankless model so the combustion air piping could be removed and the air boundary could be resored to the ceiling rather than the closet door. This was a crucial step in sealing the home as this was, by far, the leakiest area of the home.
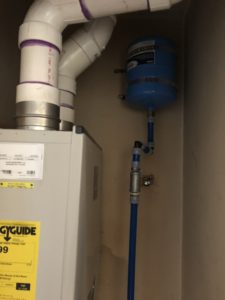
Upon Completion of the Project we were able to fix all of the proposed problems initially diagnosed upon completion of the ACCA Manual J and D Load Calculation and the Energy Audit. The home leakage rate was reduced significantly. Though this project cst nearly $20,000, with our financing and rebates, it was accomplished with a down payment of less than $8,000. Call us today if you are interested in making your home more energy efficient and, more importantly, more comfortable.
John Morris
www.morrisheatandair.net
(918) 734-0040
morrisheatandair@gmail.com